10.1: Solder Bonding
- Page ID
- 3538
\( \newcommand{\vecs}[1]{\overset { \scriptstyle \rightharpoonup} {\mathbf{#1}} } \)
\( \newcommand{\vecd}[1]{\overset{-\!-\!\rightharpoonup}{\vphantom{a}\smash {#1}}} \)
\( \newcommand{\id}{\mathrm{id}}\) \( \newcommand{\Span}{\mathrm{span}}\)
( \newcommand{\kernel}{\mathrm{null}\,}\) \( \newcommand{\range}{\mathrm{range}\,}\)
\( \newcommand{\RealPart}{\mathrm{Re}}\) \( \newcommand{\ImaginaryPart}{\mathrm{Im}}\)
\( \newcommand{\Argument}{\mathrm{Arg}}\) \( \newcommand{\norm}[1]{\| #1 \|}\)
\( \newcommand{\inner}[2]{\langle #1, #2 \rangle}\)
\( \newcommand{\Span}{\mathrm{span}}\)
\( \newcommand{\id}{\mathrm{id}}\)
\( \newcommand{\Span}{\mathrm{span}}\)
\( \newcommand{\kernel}{\mathrm{null}\,}\)
\( \newcommand{\range}{\mathrm{range}\,}\)
\( \newcommand{\RealPart}{\mathrm{Re}}\)
\( \newcommand{\ImaginaryPart}{\mathrm{Im}}\)
\( \newcommand{\Argument}{\mathrm{Arg}}\)
\( \newcommand{\norm}[1]{\| #1 \|}\)
\( \newcommand{\inner}[2]{\langle #1, #2 \rangle}\)
\( \newcommand{\Span}{\mathrm{span}}\) \( \newcommand{\AA}{\unicode[.8,0]{x212B}}\)
\( \newcommand{\vectorA}[1]{\vec{#1}} % arrow\)
\( \newcommand{\vectorAt}[1]{\vec{\text{#1}}} % arrow\)
\( \newcommand{\vectorB}[1]{\overset { \scriptstyle \rightharpoonup} {\mathbf{#1}} } \)
\( \newcommand{\vectorC}[1]{\textbf{#1}} \)
\( \newcommand{\vectorD}[1]{\overrightarrow{#1}} \)
\( \newcommand{\vectorDt}[1]{\overrightarrow{\text{#1}}} \)
\( \newcommand{\vectE}[1]{\overset{-\!-\!\rightharpoonup}{\vphantom{a}\smash{\mathbf {#1}}}} \)
\( \newcommand{\vecs}[1]{\overset { \scriptstyle \rightharpoonup} {\mathbf{#1}} } \)
\( \newcommand{\vecd}[1]{\overset{-\!-\!\rightharpoonup}{\vphantom{a}\smash {#1}}} \)
\(\newcommand{\avec}{\mathbf a}\) \(\newcommand{\bvec}{\mathbf b}\) \(\newcommand{\cvec}{\mathbf c}\) \(\newcommand{\dvec}{\mathbf d}\) \(\newcommand{\dtil}{\widetilde{\mathbf d}}\) \(\newcommand{\evec}{\mathbf e}\) \(\newcommand{\fvec}{\mathbf f}\) \(\newcommand{\nvec}{\mathbf n}\) \(\newcommand{\pvec}{\mathbf p}\) \(\newcommand{\qvec}{\mathbf q}\) \(\newcommand{\svec}{\mathbf s}\) \(\newcommand{\tvec}{\mathbf t}\) \(\newcommand{\uvec}{\mathbf u}\) \(\newcommand{\vvec}{\mathbf v}\) \(\newcommand{\wvec}{\mathbf w}\) \(\newcommand{\xvec}{\mathbf x}\) \(\newcommand{\yvec}{\mathbf y}\) \(\newcommand{\zvec}{\mathbf z}\) \(\newcommand{\rvec}{\mathbf r}\) \(\newcommand{\mvec}{\mathbf m}\) \(\newcommand{\zerovec}{\mathbf 0}\) \(\newcommand{\onevec}{\mathbf 1}\) \(\newcommand{\real}{\mathbb R}\) \(\newcommand{\twovec}[2]{\left[\begin{array}{r}#1 \\ #2 \end{array}\right]}\) \(\newcommand{\ctwovec}[2]{\left[\begin{array}{c}#1 \\ #2 \end{array}\right]}\) \(\newcommand{\threevec}[3]{\left[\begin{array}{r}#1 \\ #2 \\ #3 \end{array}\right]}\) \(\newcommand{\cthreevec}[3]{\left[\begin{array}{c}#1 \\ #2 \\ #3 \end{array}\right]}\) \(\newcommand{\fourvec}[4]{\left[\begin{array}{r}#1 \\ #2 \\ #3 \\ #4 \end{array}\right]}\) \(\newcommand{\cfourvec}[4]{\left[\begin{array}{c}#1 \\ #2 \\ #3 \\ #4 \end{array}\right]}\) \(\newcommand{\fivevec}[5]{\left[\begin{array}{r}#1 \\ #2 \\ #3 \\ #4 \\ #5 \\ \end{array}\right]}\) \(\newcommand{\cfivevec}[5]{\left[\begin{array}{c}#1 \\ #2 \\ #3 \\ #4 \\ #5 \\ \end{array}\right]}\) \(\newcommand{\mattwo}[4]{\left[\begin{array}{rr}#1 \amp #2 \\ #3 \amp #4 \\ \end{array}\right]}\) \(\newcommand{\laspan}[1]{\text{Span}\{#1\}}\) \(\newcommand{\bcal}{\cal B}\) \(\newcommand{\ccal}{\cal C}\) \(\newcommand{\scal}{\cal S}\) \(\newcommand{\wcal}{\cal W}\) \(\newcommand{\ecal}{\cal E}\) \(\newcommand{\coords}[2]{\left\{#1\right\}_{#2}}\) \(\newcommand{\gray}[1]{\color{gray}{#1}}\) \(\newcommand{\lgray}[1]{\color{lightgray}{#1}}\) \(\newcommand{\rank}{\operatorname{rank}}\) \(\newcommand{\row}{\text{Row}}\) \(\newcommand{\col}{\text{Col}}\) \(\renewcommand{\row}{\text{Row}}\) \(\newcommand{\nul}{\text{Nul}}\) \(\newcommand{\var}{\text{Var}}\) \(\newcommand{\corr}{\text{corr}}\) \(\newcommand{\len}[1]{\left|#1\right|}\) \(\newcommand{\bbar}{\overline{\bvec}}\) \(\newcommand{\bhat}{\widehat{\bvec}}\) \(\newcommand{\bperp}{\bvec^\perp}\) \(\newcommand{\xhat}{\widehat{\xvec}}\) \(\newcommand{\vhat}{\widehat{\vvec}}\) \(\newcommand{\uhat}{\widehat{\uvec}}\) \(\newcommand{\what}{\widehat{\wvec}}\) \(\newcommand{\Sighat}{\widehat{\Sigma}}\) \(\newcommand{\lt}{<}\) \(\newcommand{\gt}{>}\) \(\newcommand{\amp}{&}\) \(\definecolor{fillinmathshade}{gray}{0.9}\)The soldering process depends on molten solder flowing into all the microscopic surface imperfections of the metals to be soldered and even penetrating very slightly below their surface. In this process, a chemical reaction occurs in which the solder actually melts some of the metals and alloys with them. Upon cooling, this combination of penetration and alloying results in a very strong bond between the solder and metal. When two pieces of metal are soldered together, a thin layer of solder adheres between them and completes the connection.
The process of surface penetration and alloying is known as wetting of the host metals (Figure 1). Some metals are very receptive to wetting and can readily be soldered, while others are non-receptive and cannot be soldered at all. Copper is very receptive to wetting by tin/lead solders. Tin also wets readily, as do silver and gold, but to a lesser extent. Solder wetting is displayed by a smooth, shiny flow of solder onto the metal surface. The process is often called tinning. Metals such as aluminum and iron will not wet properly. The solder forms stubborn flecks and balls and fails to penetrate or adhere. Effective solder bonding of these metals is not possible.
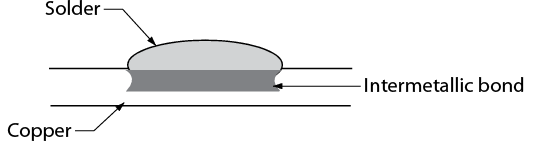
- Wetting action
Solder flux
Solder wetting of metal is severely curtailed by the presence of surface oxides. This is one of the reasons aluminum cannot be tinned and soldered. Its surface is oxidized almost instantly by the presence of atmospheric oxygen. A clean, oxide-free surface cannot be obtained for soldering. Oxidization also restricts wetting of copper, so any copper parts to be soldered should be as clean as possible. Fortunately, copper oxidizes rather slowly, so surfaces cleaned by scraping or sanding will remain pure copper for some time before a tarnishing film of copper oxide reforms.
Unfortunately, oxidization is hastened by heat. Application of a heated soldering iron or molten solder will start surface oxidation, even on a freshly cleaned surface. For this reason, it is very hard to solder even clean copper without applying a soldering flux.
The primary function of a soldering flux is to eliminate oxidation during the soldering process. Flux melts and flows when heated, effectively sealing the surfaces against the entry of oxygen. Flux also lowers the surface tension of the molten solder, allowing it to flow and spread more easily. Flux contains a small quantity of an active antioxidant material, which serves as a mild cleaner to remove any surface tarnish.
Historically, soldering flux has been caustic liquids or pastes containing acids. This is because part of their function has been to scour and roughen the surfaces. The problem with acid flux is that it never completely vaporizes during heating and continues to corrode the metal surfaces indefinitely.
The flux most commonly used in electric soldering is rosin. Rosin is an organic material derived from certain tree saps. It is non-corrosive, reasonably non-toxic, and readily liquefied by heat. Its residues are also easily removed after soldering. Rosin flux is usually a continuous single or multiple core inside the wire solder (Figure 2). Because it melts at a much lower temperature than solder, rosin is readily dispersed onto the job both before and during the melting of the solder. Low-odour solder and solders without flux are available.
Figure \(\PageIndex{1}\): (CC BY-NC-SA; BC Industry Training Authority) - Flux-cored solder wire
Rosin core solder is the only kind you should use in electric work. Never use acid core or other solder containing corrosive flux. Never use any form of paste or liquid flux containing acid. Not only will the ongoing corrosion eventually cause mechanical deterioration, it will rapidly destroy the connection’s ability to conduct current.
Composition of solder
Solder is an alloy of different metals, commonly tin and lead, that have a lower melting point than the base metal. Both metals are reasonably good electrical conductors. The ratio of tin to lead has a great deal to do with the melting point and hardness of solder and also with its conductivity. Tin melts at about 327°C (620°F) and lead at about 232°C (450°F). When these metals are combined, the melting point of the mixture goes down. The melting point varies with the ratio of tin to lead, with the lowest occurring at about 183°C (360°F) for a 63/37 tin-lead mixture.
This lowest melting temperature is called the eutectic point. It marks the temperature at which the solder changes directly from solid to liquid with no semi-liquid or plastic state in between. Since a narrow plastic state is desirable in soldering operations, a 60/40 mix is very common. This raises the melting point slightly to about 188°C (370°F) and gives a temperature range for plasticity of about 4°C to 6°C (40°F to 43°F). It also produces optimum conduction characteristics and hardness for electronics soldering.
Note that the ratios for solder composition always state the tin content first.
60/40 solder is composed of 60% tin and 40% lead (by weight).Wire solder is available in a variety of diameters. Which to use depends on the sizes of the component leads and terminals to be soldered. Diameters of 0.75 mm (1/16ø) and 0.38 mm (1/32ø) are the most commonly used sizes.