7.1: Chapter 7: Lean Manufacturing
- Page ID
- 2284
\( \newcommand{\vecs}[1]{\overset { \scriptstyle \rightharpoonup} {\mathbf{#1}} } \)
\( \newcommand{\vecd}[1]{\overset{-\!-\!\rightharpoonup}{\vphantom{a}\smash {#1}}} \)
\( \newcommand{\id}{\mathrm{id}}\) \( \newcommand{\Span}{\mathrm{span}}\)
( \newcommand{\kernel}{\mathrm{null}\,}\) \( \newcommand{\range}{\mathrm{range}\,}\)
\( \newcommand{\RealPart}{\mathrm{Re}}\) \( \newcommand{\ImaginaryPart}{\mathrm{Im}}\)
\( \newcommand{\Argument}{\mathrm{Arg}}\) \( \newcommand{\norm}[1]{\| #1 \|}\)
\( \newcommand{\inner}[2]{\langle #1, #2 \rangle}\)
\( \newcommand{\Span}{\mathrm{span}}\)
\( \newcommand{\id}{\mathrm{id}}\)
\( \newcommand{\Span}{\mathrm{span}}\)
\( \newcommand{\kernel}{\mathrm{null}\,}\)
\( \newcommand{\range}{\mathrm{range}\,}\)
\( \newcommand{\RealPart}{\mathrm{Re}}\)
\( \newcommand{\ImaginaryPart}{\mathrm{Im}}\)
\( \newcommand{\Argument}{\mathrm{Arg}}\)
\( \newcommand{\norm}[1]{\| #1 \|}\)
\( \newcommand{\inner}[2]{\langle #1, #2 \rangle}\)
\( \newcommand{\Span}{\mathrm{span}}\) \( \newcommand{\AA}{\unicode[.8,0]{x212B}}\)
\( \newcommand{\vectorA}[1]{\vec{#1}} % arrow\)
\( \newcommand{\vectorAt}[1]{\vec{\text{#1}}} % arrow\)
\( \newcommand{\vectorB}[1]{\overset { \scriptstyle \rightharpoonup} {\mathbf{#1}} } \)
\( \newcommand{\vectorC}[1]{\textbf{#1}} \)
\( \newcommand{\vectorD}[1]{\overrightarrow{#1}} \)
\( \newcommand{\vectorDt}[1]{\overrightarrow{\text{#1}}} \)
\( \newcommand{\vectE}[1]{\overset{-\!-\!\rightharpoonup}{\vphantom{a}\smash{\mathbf {#1}}}} \)
\( \newcommand{\vecs}[1]{\overset { \scriptstyle \rightharpoonup} {\mathbf{#1}} } \)
\( \newcommand{\vecd}[1]{\overset{-\!-\!\rightharpoonup}{\vphantom{a}\smash {#1}}} \)
\(\newcommand{\avec}{\mathbf a}\) \(\newcommand{\bvec}{\mathbf b}\) \(\newcommand{\cvec}{\mathbf c}\) \(\newcommand{\dvec}{\mathbf d}\) \(\newcommand{\dtil}{\widetilde{\mathbf d}}\) \(\newcommand{\evec}{\mathbf e}\) \(\newcommand{\fvec}{\mathbf f}\) \(\newcommand{\nvec}{\mathbf n}\) \(\newcommand{\pvec}{\mathbf p}\) \(\newcommand{\qvec}{\mathbf q}\) \(\newcommand{\svec}{\mathbf s}\) \(\newcommand{\tvec}{\mathbf t}\) \(\newcommand{\uvec}{\mathbf u}\) \(\newcommand{\vvec}{\mathbf v}\) \(\newcommand{\wvec}{\mathbf w}\) \(\newcommand{\xvec}{\mathbf x}\) \(\newcommand{\yvec}{\mathbf y}\) \(\newcommand{\zvec}{\mathbf z}\) \(\newcommand{\rvec}{\mathbf r}\) \(\newcommand{\mvec}{\mathbf m}\) \(\newcommand{\zerovec}{\mathbf 0}\) \(\newcommand{\onevec}{\mathbf 1}\) \(\newcommand{\real}{\mathbb R}\) \(\newcommand{\twovec}[2]{\left[\begin{array}{r}#1 \\ #2 \end{array}\right]}\) \(\newcommand{\ctwovec}[2]{\left[\begin{array}{c}#1 \\ #2 \end{array}\right]}\) \(\newcommand{\threevec}[3]{\left[\begin{array}{r}#1 \\ #2 \\ #3 \end{array}\right]}\) \(\newcommand{\cthreevec}[3]{\left[\begin{array}{c}#1 \\ #2 \\ #3 \end{array}\right]}\) \(\newcommand{\fourvec}[4]{\left[\begin{array}{r}#1 \\ #2 \\ #3 \\ #4 \end{array}\right]}\) \(\newcommand{\cfourvec}[4]{\left[\begin{array}{c}#1 \\ #2 \\ #3 \\ #4 \end{array}\right]}\) \(\newcommand{\fivevec}[5]{\left[\begin{array}{r}#1 \\ #2 \\ #3 \\ #4 \\ #5 \\ \end{array}\right]}\) \(\newcommand{\cfivevec}[5]{\left[\begin{array}{c}#1 \\ #2 \\ #3 \\ #4 \\ #5 \\ \end{array}\right]}\) \(\newcommand{\mattwo}[4]{\left[\begin{array}{rr}#1 \amp #2 \\ #3 \amp #4 \\ \end{array}\right]}\) \(\newcommand{\laspan}[1]{\text{Span}\{#1\}}\) \(\newcommand{\bcal}{\cal B}\) \(\newcommand{\ccal}{\cal C}\) \(\newcommand{\scal}{\cal S}\) \(\newcommand{\wcal}{\cal W}\) \(\newcommand{\ecal}{\cal E}\) \(\newcommand{\coords}[2]{\left\{#1\right\}_{#2}}\) \(\newcommand{\gray}[1]{\color{gray}{#1}}\) \(\newcommand{\lgray}[1]{\color{lightgray}{#1}}\) \(\newcommand{\rank}{\operatorname{rank}}\) \(\newcommand{\row}{\text{Row}}\) \(\newcommand{\col}{\text{Col}}\) \(\renewcommand{\row}{\text{Row}}\) \(\newcommand{\nul}{\text{Nul}}\) \(\newcommand{\var}{\text{Var}}\) \(\newcommand{\corr}{\text{corr}}\) \(\newcommand{\len}[1]{\left|#1\right|}\) \(\newcommand{\bbar}{\overline{\bvec}}\) \(\newcommand{\bhat}{\widehat{\bvec}}\) \(\newcommand{\bperp}{\bvec^\perp}\) \(\newcommand{\xhat}{\widehat{\xvec}}\) \(\newcommand{\vhat}{\widehat{\vvec}}\) \(\newcommand{\uhat}{\widehat{\uvec}}\) \(\newcommand{\what}{\widehat{\wvec}}\) \(\newcommand{\Sighat}{\widehat{\Sigma}}\) \(\newcommand{\lt}{<}\) \(\newcommand{\gt}{>}\) \(\newcommand{\amp}{&}\) \(\definecolor{fillinmathshade}{gray}{0.9}\)OBJECTIVE
After completing this unit, you should be able to:
- Apply 5S in any Machine shop.
- Describe Kaizen Concept.
- Describe Implementing Lean Manufacturing.
Lean 5S:
“5S” is a method of workplace organization that consists of five words: Sort, Set in order, Shine, Standardize, and Sustain. All of these words begin with the letter S. These five components describe how to store items and maintain the new order. When making decisions, employees discuss standardization, which will make the work process clear among the workers. By doing this, each employee will feel ownership of the process.
Phase 0: Safety
It is often assumed that a properly executed 5S program will improve workplace safety, but this is false. Safety is not an option; it’s a priority.
Phase 1: Sort
Review all items in the workplace, keeping only what is needed.
Phase 2: Straighten
Everything should have a place and be in place. Items should be divided and labeled. Everything should be arranged thoughtfully. Employees should not have to bend over repetitively. Place equipment near where it is used. This step is a part of why lean 5s is not considered “standardized cleanup”.
Phase 3: Shine
Make sure that the workplace is clean and neat. By doing this, it will be easier to be aware of where things are and where they should be. After working, clean the workspace and return everything to its former position. Keeping the workplace clean should be integrated into the daily routine.
Phase 4: Standardize
Standardize work procedures and make them consistent. Every worker should be aware of what their responsibilities are when following the first three steps.
Phase 5: Sustain
Assess and maintain the standards. The aforementioned steps should become the new norm in operation. Do not gradually revert to the old ways. When taking part of the new procedure, think of ways to improve. Review the first four steps when new tools or output requirements are presented.
Kaizen
While the lean 5S process focuses on the removal of waste, Kaizen focuses on the practice of continuous improvement. Like lean 5S, Kaizen identifies three main aspects of the workplace: Muda (wastes), Mura (inconsistencies) and Muri (strain on people & machines). However, the Kaizen step-by-step process is more extensive that the lean 5S process.
The Kaizen process overview:
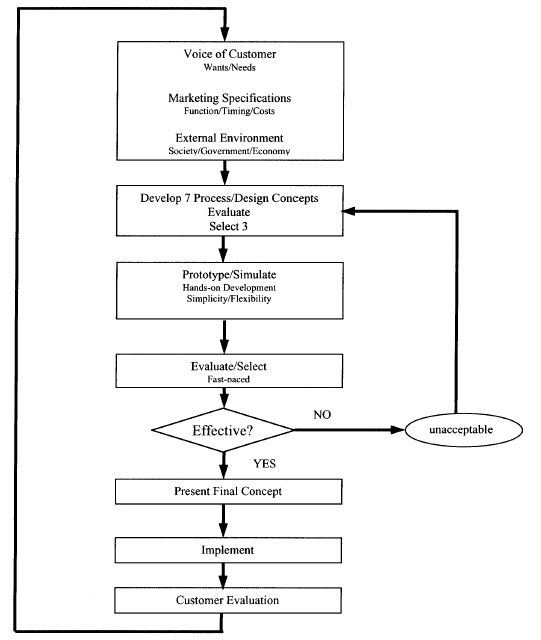
1. Identify a problem.
2. Form a team.
3. Gather information from internal and external customers, and determine goals for the project.
4. Review the current situation or process.
5. Brainstorm and consider seven possible alternatives.
6. Decide the three best alternatives of the seven.
7. Simulate and evaluate these alternatives before implementation.
8. Present the idea and suggestions to managers.
9. Physically implement the Kaizen results and take account of the effects.
Lean manufacturing improves as time goes one, so it is important to continue education about maintaining standards. It is crucial to change the standards and train workers when presented with new equipment or rules.
Lean
Think of a maintenance department as serving internal customers: the various departments and workers in the company.
Lean is different from the traditional western, mass production model that relies on economies of scale to create profits. The more you make the cheaper the product will become, the greater the potential profit margin. It is based on predictions of customer needs, or creating customer needs. It has difficulty dealing with unusual changes in demand.
Lean production responds to proven customer demand. Pull processing – the customer pulls production. In a mass system the producer pushes product onto the market, push processing.
Building a long-term culture that focuses on improvement.
Respect for workers better trained and educated, more flexible
Lean is a philosophy that focuses on the following:
- Meeting customer needs
- Continuous, gradual improvement
- Making continuously better products
- Valuing the input of workers
- Taking the long term view
- Eliminating mistakes
- Eliminating waste
Wastes: using too many resources (materials, time, energy, space, money, human resources, poor instructions)
Wastes:
- Overproduction
- Defects
- Unnecessary processing
- Waiting (wasting time)
- Wasting human time and talent
- Too many steps or moving aroundExcessive transportation
- Excessive inventory
Lean production includes working with suppliers, sub contractors, and sellers to stream line the whole process.
The goal is that production would flow smoothly avoiding costly starts and stops.
The idea is called just in time “produce only what is needed, when it is needed, and only in the quantity needed.” Production process must be flexible and fast.
Inventory = just what you need
In mass production = just in case. Extra supplies and products are stored just in case they are needed.
Terminology:
Process simplification – a process outside of the flow of production
Defects – the mass production system does inspection at the end of production to catch defects before they are shipped. The problem is that the resources have already been “spent” to make the waste product” Try to prevent problems immediately, as they happen, then prevent them. Inspection during production, at each stage of production.
Safety – hurt time is waste time
Information – need the right information at the right time (too much, too little, too late)
Principles:
Poka-yoke – mistake proof determining the cause of problems and then removing the cause to prevent further errors
Judgment errors – finding problems after the process
Informative inspections – analyzing data from inspections during the process
Source inspections – inspection before the process begins to prevent errors.
MEAN LEAN
One of the terms applied to a simply cost cutting, job cutting interpretation of Lean is Mean Lean. Often modern manager think they are doing lean without understanding the importance of workers and long term relationships.
Reliability Centered Maintenance
Reliablity centered maintenance is a system for designing a cost effective maintenance program. It can be a detailed complex, computer, statistically driven, but at its basics it is fairly simple. Its ideas can be applied to designing and operating a PM system, and can also guide your learning as you do maintenance, troubleshooting, repair and energy work.
These are core principles of RCM. These nine fundamental concepts are:
- Failures happen.
- Not all failures have the same probability
- Not all failures have the same consequences
- Simple components wear out, complex systems break down
- Good maintenance provides required functionality for lowest practicable cost
- Maintenance can only achieve inherent design reliability of the equipment
- Unnecessary maintenance takes resources away from necessary maintenance
- Good maintenance programs undergo continuous improvement.
Maintenance consists of all actions taken to ensure that components, equipment, and systems provide their intended functions when required.
An RCM system is based on answering the following questions:
1. What are the functions and desired standards of performance of the equipment?
2. In what ways can it fail to fulfil its functions? (Which are the most likely failures? How likely is each type of failure? Will the failures be obvious? Can it be a partial failure?)
3. What causes each failure?
4. What happens when each failure occurs? (What is the risk, danger etc.?)
5. In what way does each failure matter? What are the consequences of a full or partial failure?
6. What can be done to predict or prevent each failure? What will it cost to predict or prevent each failure?
7. What should be done if a suitable proactive task cannot be found (default actions) (no task might be available, or it might be too costly for the risk)?
Equipment is studied in the context of where when and how it is being used
All maintenance actions can be classified into one of the following categories:
- Corrective Maintenance – Restore lost or degraded function
- Preventive Maintenance – Minimizes opportunity for function to fail
- Alterative Maintenance – Eliminate unsatisfactory condition by changing system design or use
Within the category of preventive maintenance all tasks accomplished can be described as belonging to one of five (5) major task types:
- Condition Directed – Renew life based on measured condition compared to a standard
- Time Directed – Renew life regardless of condition
- Failure Finding – Determine whether failure has occurred
- Servicing – Add/replenish consumables
- Lubrication – Oil, grease or otherwise lubricate
We do maintenance because we believe that hardware reliability degrades with age, but that we can do something to restore or maintain the original reliability that pays for itself.
RCM is reliability-centered. Its objective is to maintain the inherent reliability of the system or equipment design, recognizing that changes in inherent reliability may be achieved only through design changes. We must understand that the equipment or system must be studied in the situation in which it is working.
Implementing Lean Manufacturing
Analyze each step in the original process before making change
Lean manufacturing main focuses is on cost reduction and increases in turnover and eliminating activities that do not add value to the manufacturing process. Basically what lean manufacturing does is help companies to achieve targeted production, as well as other things, by introducing tools and techniques that are easy to apply and maintain. What these tools and techniques are doing is reducing and eliminating waste, things that are not needed in the manufacturing process.
Manufacturing engineers set out to use the six-sigma DMAIC (Design, Measure, Analyze, Improve, Control) methodology—in conjunction with lean manufacturing—to meet customer requirements related to the production of tubes.
Manufacturing engineers were charged with designing a new process layout of the tube production line. The objectives for project were including:
- Improved quality
- Decreased scrap
- Delivery to the point of use
- Smaller lot sizes
- Implementation of a pull system
- Better feedback
- Increased production
- Individual Responsibility
- Decreased WIP
- Dine flexibility
Before making changes, the team analyze each step in the original layout of the tube production line process.
1. There try to understand the original state process, identify the problem area, unnecessary step and non value added.
2. After mapping the process, the lean team collected data from the Material Review Board (MRB) bench to measure and analyze major types of defects . To better understand the process, the team also did a time study for 20 days period production run.
In the original state, the tube line consisted of one operator and four operations, separated into two stations by a large table using a push system. The table acted as a separator between the second and third operation.
The first problem discovered was the line’s unbalanced . The first station was used about 70% of the time. Operators at the second station were spending a lot of their time waiting between cycle times. By combining stations one and two, room for improvement became evident with respect to individual responsibility, control of inventory by the operator, and immediate feedback when a problem occurred. The time study and the department layout reflect these findings.
A second problem was recognized. Because of the process flow, the production rate did not allow the production schedule to be met with two stations. Because operators lost track of machine cycles, machines were waiting for operator attention. Operators also tried to push parts through the first station—the bottleneck operation in the process—and then continued to manufacture the parts at the last two operations. Typically, long runs of WIP built up, and quality problems were not caught until a lot number of defective pieces were produced.
The original state data were taken from the last 20 days before the change. The teams analyze each step in the original and making changes. The findings of the time study on the original process provided the basis for reducing cycle time, balancing the line, designing the using Just In Time kanbans and scheduling, improve quality, decrease lot size and WIP , and improve flow. The new process data were taken starting one month after implementation. This delay gave the machine operators an opportunity to train and get to with the new process layout system.
With the U shaped cell design; The parts meet all the customer requirement. Table in the original process was removed ,almost eliminating WIP. With the reducing WIP and increasing production.
Some of the concepts used to improve the process included total employee involvement (TEI), smaller lot sizes, scheduling, point of use inventory, and improved layout. All employees and supervisors in the department were involved in all phases of the project. Their ideas and suggestions were incorporated in the planning and implementation process to gain wider acceptance of the changes to the process. Smaller lot sizes were introduced to minimize the number of parts produced before defects were detected. Kanbans were introduced (in the form of material handling racks) to control WIP and to implement a pull system. And the cell layout decreased travel between operations.
Operators were authorized to stop the line when problems arose. In the original-state , the operators were still continue running parts when a operation was down. With kanban
control, the layout eliminated the ability to store WIP, requiring the operator to shut down the entire line. The cell layout provides excellent opportunities for improving communication between operators about problems and adjustments, to achieve better quality.
Day-to-day inspection of the original-state process the operators spent a lot of time either waiting for material-handling person, or performing as a material handling. With the U-shaped cell, delivery to the point of use is more better for the operator. The operator places boxes of raw material on six moveable roller carts, where it’s easily to get. The six boxes are enough to last a 24-hr period.
To reduce setup times, tools needed for machine repair and adjustments are located in the cell. The screws are not standardized; tools are set up in order of increasing size to quickly identify the proper tool.
For three months the process was monitored to verify that it was in control. Comparison of time studies from the original-state and the implemented layout demonstrated an increase in production from 300 to 514 finished products per shift. The new layout eliminated double handling between the second and third operations, as well as at the packing step. It also reduced throughout time by making it easier to cycle all four operations in a pull-system order. Customer demand was met by two shifts, which reduced the labor cost.
The results of the redesign are as follows:
- WIP decreased by 97%
- Production increased 72%
- Scrap was reduced by 43%
- Machine utilization increased by 50%
- Labor utilization increased by 25%
- Labor costs were reduced by 33%
- Sigma level increased from 2.6 to 2.8
This project yielded reduced labor and scrap costs, and allowed the organization to do a better job of making deliveries on time, while allowing a smaller finished-goods inventory. Daily production numbers and single-part cycle time served as a benchmark for monitoring progress towards the goal. Although the sigma level increase , the 43% reduction in defects, 97% reduction in WIP, and production increase of 72% contributed to the project objective.
Implementing lean is a never ending process; this is what continuous improvement is all
about. When you get one aspect of lean implemented, it can always be improved. Don’t get hung up on it, but don’t let things slip back to the starting point. There will always be time to go back and refine some of the processes.
Before Lean Manufacturing was implemented at Nypro Oregon Inc., we would operate using traditional manufacturing. Traditional manufacturing consists of producing all of a given product for the marketplace so as to never let the equipment idle. These goods them need to be warehoused or shipped out to a customer who may not be ready for them. If more is produced than can be sold, the products will be sold at a deep discount (often a loss) or simply scrapped. This can add up to an enormous amount waste. After implementing Lean Manufacturing concepts, our company uses just in time. Just in time refers to producing and delivering good in the amount required when the customer requires it and not before. In lean Manufacturing, the manufacture only produces what the customer wants, when they want it. This often a much more cost effective way of manufacturing when compared to high priced, high volume equipment.
Unit Test:
1. What is 5S?
2. Please Explain each “S” of the 5S.
3. Please Explain Kaizen concept.
4. What is the Pull processing?
5. What is the Poka-yoke?
6. What is the six-sigma DMAIC?
7. What is the objectives for a new process layout of the tube production line?
8. Before making changes, The Manufacturing engineers team do what first?
9. Please lists the results of the redesign.
10. The key to implementing lean new idea or concept is to do what?
CHAPTER ATTRIBUTION INFORMATION
This chapter was derived from the following sources.
- Lean 5S derived from Lean Manufacturing by various authors, CC:BY-SA 3.0.
- Kaizen derived from A Kaizen Based Approach for Cellular Manufacturing System Design: A Case Study by VirginiaTech, CC:BY-SA 4.0.
- Kaizen (image) derived from A Kaizen Based Approach for Cellular Manufacturing System Design: A Case Study by VirginiaTech, CC:BY-SA 4.0.