7.C: Lab Safety - Industrial Safety and Manufacturing
- Page ID
- 18247
\( \newcommand{\vecs}[1]{\overset { \scriptstyle \rightharpoonup} {\mathbf{#1}} } \)
\( \newcommand{\vecd}[1]{\overset{-\!-\!\rightharpoonup}{\vphantom{a}\smash {#1}}} \)
\( \newcommand{\id}{\mathrm{id}}\) \( \newcommand{\Span}{\mathrm{span}}\)
( \newcommand{\kernel}{\mathrm{null}\,}\) \( \newcommand{\range}{\mathrm{range}\,}\)
\( \newcommand{\RealPart}{\mathrm{Re}}\) \( \newcommand{\ImaginaryPart}{\mathrm{Im}}\)
\( \newcommand{\Argument}{\mathrm{Arg}}\) \( \newcommand{\norm}[1]{\| #1 \|}\)
\( \newcommand{\inner}[2]{\langle #1, #2 \rangle}\)
\( \newcommand{\Span}{\mathrm{span}}\)
\( \newcommand{\id}{\mathrm{id}}\)
\( \newcommand{\Span}{\mathrm{span}}\)
\( \newcommand{\kernel}{\mathrm{null}\,}\)
\( \newcommand{\range}{\mathrm{range}\,}\)
\( \newcommand{\RealPart}{\mathrm{Re}}\)
\( \newcommand{\ImaginaryPart}{\mathrm{Im}}\)
\( \newcommand{\Argument}{\mathrm{Arg}}\)
\( \newcommand{\norm}[1]{\| #1 \|}\)
\( \newcommand{\inner}[2]{\langle #1, #2 \rangle}\)
\( \newcommand{\Span}{\mathrm{span}}\) \( \newcommand{\AA}{\unicode[.8,0]{x212B}}\)
\( \newcommand{\vectorA}[1]{\vec{#1}} % arrow\)
\( \newcommand{\vectorAt}[1]{\vec{\text{#1}}} % arrow\)
\( \newcommand{\vectorB}[1]{\overset { \scriptstyle \rightharpoonup} {\mathbf{#1}} } \)
\( \newcommand{\vectorC}[1]{\textbf{#1}} \)
\( \newcommand{\vectorD}[1]{\overrightarrow{#1}} \)
\( \newcommand{\vectorDt}[1]{\overrightarrow{\text{#1}}} \)
\( \newcommand{\vectE}[1]{\overset{-\!-\!\rightharpoonup}{\vphantom{a}\smash{\mathbf {#1}}}} \)
\( \newcommand{\vecs}[1]{\overset { \scriptstyle \rightharpoonup} {\mathbf{#1}} } \)
\( \newcommand{\vecd}[1]{\overset{-\!-\!\rightharpoonup}{\vphantom{a}\smash {#1}}} \)
\(\newcommand{\avec}{\mathbf a}\) \(\newcommand{\bvec}{\mathbf b}\) \(\newcommand{\cvec}{\mathbf c}\) \(\newcommand{\dvec}{\mathbf d}\) \(\newcommand{\dtil}{\widetilde{\mathbf d}}\) \(\newcommand{\evec}{\mathbf e}\) \(\newcommand{\fvec}{\mathbf f}\) \(\newcommand{\nvec}{\mathbf n}\) \(\newcommand{\pvec}{\mathbf p}\) \(\newcommand{\qvec}{\mathbf q}\) \(\newcommand{\svec}{\mathbf s}\) \(\newcommand{\tvec}{\mathbf t}\) \(\newcommand{\uvec}{\mathbf u}\) \(\newcommand{\vvec}{\mathbf v}\) \(\newcommand{\wvec}{\mathbf w}\) \(\newcommand{\xvec}{\mathbf x}\) \(\newcommand{\yvec}{\mathbf y}\) \(\newcommand{\zvec}{\mathbf z}\) \(\newcommand{\rvec}{\mathbf r}\) \(\newcommand{\mvec}{\mathbf m}\) \(\newcommand{\zerovec}{\mathbf 0}\) \(\newcommand{\onevec}{\mathbf 1}\) \(\newcommand{\real}{\mathbb R}\) \(\newcommand{\twovec}[2]{\left[\begin{array}{r}#1 \\ #2 \end{array}\right]}\) \(\newcommand{\ctwovec}[2]{\left[\begin{array}{c}#1 \\ #2 \end{array}\right]}\) \(\newcommand{\threevec}[3]{\left[\begin{array}{r}#1 \\ #2 \\ #3 \end{array}\right]}\) \(\newcommand{\cthreevec}[3]{\left[\begin{array}{c}#1 \\ #2 \\ #3 \end{array}\right]}\) \(\newcommand{\fourvec}[4]{\left[\begin{array}{r}#1 \\ #2 \\ #3 \\ #4 \end{array}\right]}\) \(\newcommand{\cfourvec}[4]{\left[\begin{array}{c}#1 \\ #2 \\ #3 \\ #4 \end{array}\right]}\) \(\newcommand{\fivevec}[5]{\left[\begin{array}{r}#1 \\ #2 \\ #3 \\ #4 \\ #5 \\ \end{array}\right]}\) \(\newcommand{\cfivevec}[5]{\left[\begin{array}{c}#1 \\ #2 \\ #3 \\ #4 \\ #5 \\ \end{array}\right]}\) \(\newcommand{\mattwo}[4]{\left[\begin{array}{rr}#1 \amp #2 \\ #3 \amp #4 \\ \end{array}\right]}\) \(\newcommand{\laspan}[1]{\text{Span}\{#1\}}\) \(\newcommand{\bcal}{\cal B}\) \(\newcommand{\ccal}{\cal C}\) \(\newcommand{\scal}{\cal S}\) \(\newcommand{\wcal}{\cal W}\) \(\newcommand{\ecal}{\cal E}\) \(\newcommand{\coords}[2]{\left\{#1\right\}_{#2}}\) \(\newcommand{\gray}[1]{\color{gray}{#1}}\) \(\newcommand{\lgray}[1]{\color{lightgray}{#1}}\) \(\newcommand{\rank}{\operatorname{rank}}\) \(\newcommand{\row}{\text{Row}}\) \(\newcommand{\col}{\text{Col}}\) \(\renewcommand{\row}{\text{Row}}\) \(\newcommand{\nul}{\text{Nul}}\) \(\newcommand{\var}{\text{Var}}\) \(\newcommand{\corr}{\text{corr}}\) \(\newcommand{\len}[1]{\left|#1\right|}\) \(\newcommand{\bbar}{\overline{\bvec}}\) \(\newcommand{\bhat}{\widehat{\bvec}}\) \(\newcommand{\bperp}{\bvec^\perp}\) \(\newcommand{\xhat}{\widehat{\xvec}}\) \(\newcommand{\vhat}{\widehat{\vvec}}\) \(\newcommand{\uhat}{\widehat{\uvec}}\) \(\newcommand{\what}{\widehat{\wvec}}\) \(\newcommand{\Sighat}{\widehat{\Sigma}}\) \(\newcommand{\lt}{<}\) \(\newcommand{\gt}{>}\) \(\newcommand{\amp}{&}\) \(\definecolor{fillinmathshade}{gray}{0.9}\)Hazards, Hazard Recognition, Hazard Categories
Machine operations expose workers to both physical hazards and physiological (ergonomic hazards). Using the Safety Precautions for Milling Machines and after viewing the video below on ergonomic safety, identify precautions that may reduce risk for ergonomic injury. Are the precautions identified sufficient? Can you provide additional precautions?
Video: Ergonomic Awareness-Dr. Ergo
Performance Standards and Design Standards
Some safety standards are performance driven in nature, meaning an action or activity is performed to achieve the safety objective or required protection. Other standards are design standards, meaning the safety function or requirement is assured by some design specification or feature in a system or equipment.
Referencing the Safety Precautions for Milling Machines, distinguish 'performance' precautions and 'design' precautions.
Standard Mapping
Map the ten referenced standards for machine presses to a physical hazard and then categorize as either design or performance.
Mechanical power press guarding and construction, general-
Hazards to personnel associated with broken or falling machine components. Machine components shall be designed, secured, or covered to minimize hazards caused by breakage, or loosening and falling or release of mechanical energy (i.e. broken springs).
1910.217(b)(4)(i)
The pedal mechanism shall be protected to prevent unintended operation from falling or moving objects or by accidental stepping onto the pedal.
1910.217(b)(7)(v)(a)
Each hand control shall be protected against unintended operation and arranged by design, construction, and/or separation so that the concurrent use of both hands is required to trip the press.
1910.217(b)(8)(i)
A main power disconnect switch capable of being locked only in the Off position shall be provided with every power press control system.
1910.217(b)(11)
Hydraulic equipment. The maximum anticipated working pressures in any hydraulic system on a mechanical power press shall not exceed the safe working pressure rating of any component used in that system.
1910.217(c)(3)(iv)(b)
Attachments shall be adjusted to prevent the operator from reaching into the point of operation or to withdraw the operator's hands from the point of operation before the dies close.
1910.217(c)(4)
Hand feeding tools. Hand feeding tools are intended for placing and removing materials in and from the press. Hand feeding tools are not a point of operation guard or protection device and shall not be used in lieu of the "guards" or devices required in this section.
1910.217(d)(1)(i)
Use dies and operating methods designed to control or eliminate hazards to operating personnel, and
1910.217(d)(1)(ii)
furnish and enforce the use of hand tools for freeing and removing stuck work or scrap pieces from the die, so that no employee need reach into the point of operation for such purposes.
1910.217(e)(1)(i)(A)
Conduct periodic and regular inspections of each power press to ensure that all of its parts, auxiliary equipment, and safeguards, including the clutch/brake mechanism, anti-repeat feature, and single-stroke mechanism, are in a safe operating condition and adjustment;
1910.217(e)(1)(ii)(A)
Inspect and test each press on a regular basis at least once a week to determine the condition of the clutch/brake mechanism, anti-repeat feature, and single-stroke mechanism
Automation and Robotics Lab Safety
Images
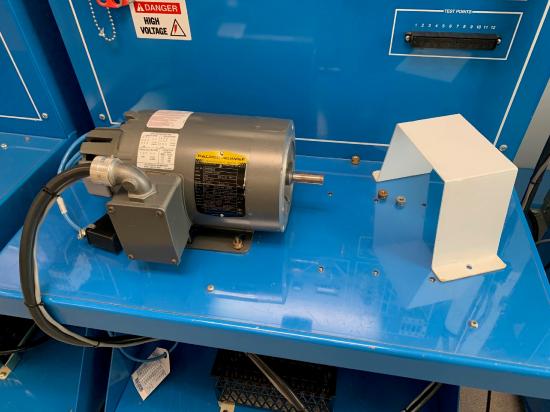

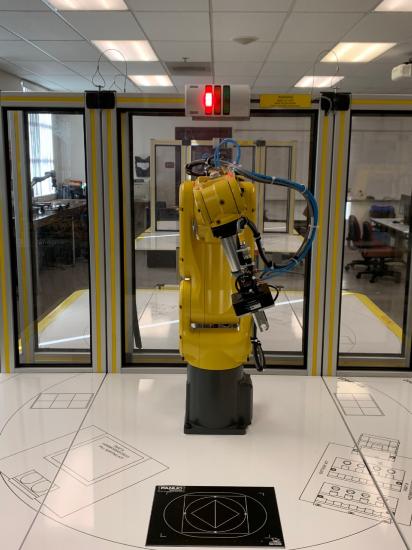




Standard Mapping - Robotics Lab Safety
There is no subpart in the OSHA safety standards that specifically calls out robotics or automation safety. However OSHA does provide guidance on Robotics Safety. Robots are machines that handle materials and manufacture parts and materials. Sections 2.1.1-2.1.5 of the FANUC Handling Tool Operations Manual are repeated below. Map each safety warning, procedure, or protocol to the standard most likely the bases for the direction. Keep in mind that OSHA's incorporation by reference of design standards and general duty clause taken together require employers to follow safety guidelines and protocols offered by the design standards and the manufacturer. For any general duty rule also add why you believe the precaution falls under general duty.
A safe workcell is essential to protect people and equipment. Observe the following guidelines to ensure that the workcell is set up safely. These suggestions are intended to supplement and not replace existing federal, state, and local laws, regulations, and guidelines that pertain to safety.
- Sponsor your personnel for training in approved FANUC Robotics training course(s) related to your application. Never permit untrained personnel to operate the robots.
- Install a lockout device that uses an access code to prevent unauthorized persons from operating the robot.
- Arrange the workcell so the operator faces the workcell and can see what is going on inside the cell. Clearly identify the work envelope of each robot in the system with floor markings, signs, and special barriers. The work envelope is the area defined by the maximum motion range of the robot, including any tooling attached to the wrist flange that extend this range
- Position all controllers outside the robot work envelope.
- Mount an adequate number of EMERGENCY STOP buttons or switches within easy reach of the operator and at critical points inside and around the outside of the workcell. flashing lights and/or audible warning devices that activate whenever the robot is operating, that is, whenever power is applied to the servo drive system. Audible warning devices shall exceed the ambient noise level at the end-use application
- Wherever possible, install safety fences to protect against unauthorized entry by personnel into the work envelope
- Install special guarding that prevents the operator from reaching into restricted areas of the work envelope
- Use presence or proximity sensing devices such as light curtains, mats, and capacitance and vision systems to enhance safety
- Periodically check the safety joints or safety clutches that can be optionally installed between the robot wrist flange and tooling. If the tooling strikes an object, these devices dislodge, remove power from the system, and help to minimize damage to the tooling and robot
- Make sure all external devices are properly filtered, grounded, shielded, and suppressed to prevent hazardous motion due to the effects of electro-magnetic interference (EMI), radio frequency interference (RFI), and electro-static discharge (ESD)
- Make provisions for power lockout/tagout at the controller
- Eliminate pinch points. Pinch points are areas where personnel could get trapped between a moving robot and other equipment
- Provide enough room inside the workcell to permit personnel to teach the robot and perform maintenance safely
- Know the path that can be used to escape from a moving robot; make sure the escape path is never blocked
Standard Mapping Table
OSHA SUBPART | FANUC SAFETY PROTOCOL |
---|---|
1910 SUBPART D | |
1910 SUBPART E | |
1910 SUBPART J | |
1910 SUBPART O | |
1910 SUBPART S | |
GENERAL DUTY CLAUSE |